Solar Panels for Manufacturing & Engineering: Powering Industrial Innovation
Solar panels offer manufacturing and engineering facilities a powerful solution to reduce energy costs and enhance sustainability. These systems can significantly lower electricity bills while providing a reliable power source for machinery, lighting, and other essential operations. Solar installations harness abundant roof space, converting sunlight into clean energy that meets high industrial demands.
Implementing solar technology in manufacturing environments brings numerous advantages. Beyond cost savings, it demonstrates a commitment to environmental responsibility, potentially boosting a company’s reputation. Solar panels also provide long-term energy security, protecting businesses from fluctuating utility prices and potential grid disruptions.
Tailored solar solutions cater to the unique needs of manufacturing and engineering facilities. Professional installers design bespoke systems that maximise energy production while considering factors like roof structure, shading, and local regulations. With proper maintenance, these systems can deliver reliable performance for decades, making them a wise investment for forward-thinking industrial operations.
Key Takeaways
- Solar panels can drastically reduce energy costs for manufacturing facilities
- Bespoke solar solutions are available to meet specific industrial requirements
- Proper installation and maintenance ensure long-term performance and benefits
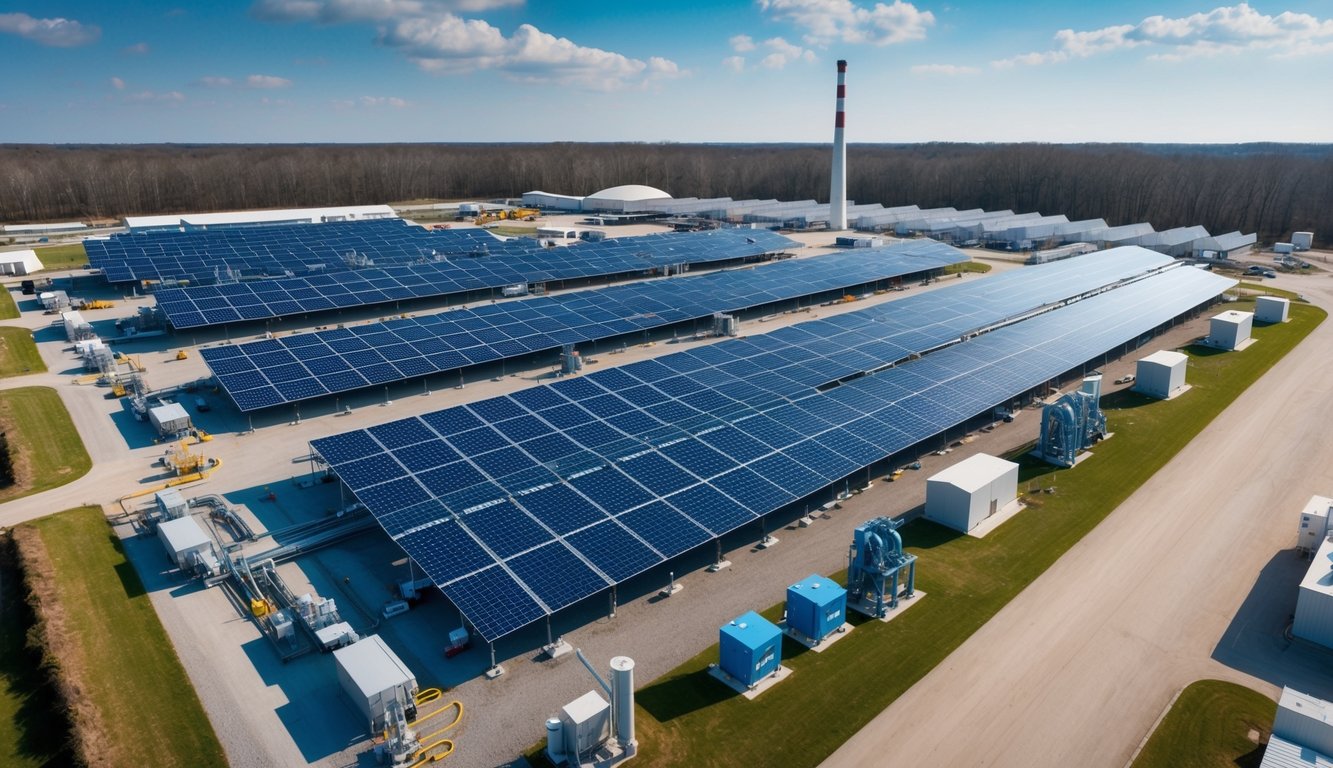
Understanding Solar Panels In Industrial Applications
Solar panels offer manufacturing facilities a sustainable energy solution with significant cost-saving potential. These systems harness sunlight to generate electricity, reducing reliance on traditional power sources and lowering operational expenses.
Types Of Solar Panels For Manufacturing
Monocrystalline and polycrystalline panels are the most common choices for industrial applications. Monocrystalline panels boast higher efficiency rates, converting up to 22% of sunlight into electricity. They perform well in limited space but come at a higher cost. Polycrystalline panels, while slightly less efficient at 15-17%, offer a more budget-friendly option.
Thin-film panels present a flexible alternative, ideal for curved surfaces or weight-restricted roofs. Though less efficient than crystalline options, their versatility makes them suitable for specific industrial settings.
Bifacial panels capture sunlight from both sides, increasing energy yield by up to 30%. These are particularly effective in areas with high ground reflectivity or when mounted on reflective surfaces.
Energy Output And Efficiency Ratings
Solar panel efficiency is crucial for industrial applications where space may be limited. Panel efficiency ratings typically range from 15% to 22%, with higher-end models reaching up to 24%.
Energy output is measured in watts, with most industrial panels ranging from 250W to 400W per panel. Factors affecting output include:
- Panel orientation
- Shading
- Temperature
- Local climate
To maximise energy production, manufacturers often opt for high-wattage panels with anti-reflective coatings and advanced cell technologies.
It’s essential to consider the panel’s degradation rate, which averages 0.5% to 0.8% annually. Quality panels maintain at least 90% of their rated output after 10 years and 80% after 25 years.
Installation Requirements For Industrial Settings
Proper installation is vital for optimal performance and longevity of industrial solar systems. Key considerations include:
- Roof integrity: The structure must support the additional weight of panels and mounting equipment. A professional assessment is crucial before installation.
- Orientation and tilt: In the UK, south-facing panels at a 30-40 degree angle typically yield the best results. However, east-west configurations can provide a more consistent power output throughout the day.
- Electrical infrastructure: Upgrading existing systems may be necessary to handle the influx of solar-generated electricity.
- Monitoring systems: Advanced monitoring tools help track performance and identify maintenance needs promptly.
- Planning permission: While many industrial installations fall under permitted development, larger systems may require approval from local authorities.
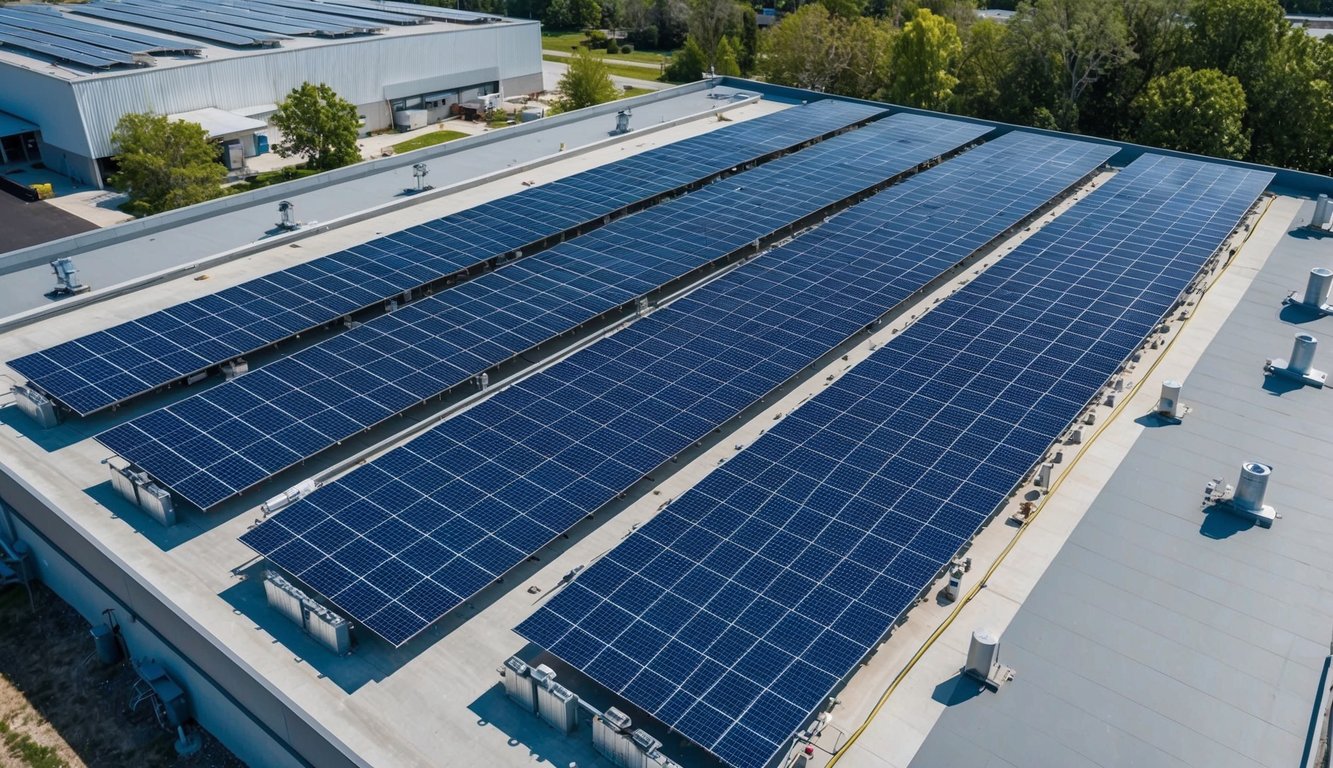
Benefits of Solar Panels in Manufacturing Facilities
Solar panels offer significant advantages for manufacturing facilities, providing cost savings, environmental benefits, and increased energy independence. These systems can transform how factories operate and contribute to a more sustainable future.
Cost Reduction and ROI Analysis
Solar panels can substantially reduce energy costs for manufacturing facilities. The initial investment typically pays off within 5-7 years, after which electricity becomes nearly free. Many factories see a 30-50% decrease in energy bills immediately after installation.
- Long-term savings: Solar panels have a lifespan of 25-30 years, providing decades of low-cost electricity.
- Government incentives: Many regions offer tax breaks, grants, or feed-in tariffs for solar adoption, further improving ROI.
- Peak shaving: Solar power can offset high-demand periods, reducing costly peak usage charges.
A table comparing energy costs before and after solar installation:
Time Frame | Without Solar | With Solar |
---|---|---|
Year 1 | £100,000 | £70,000 |
Year 5 | £110,000 | £20,000 |
Year 10 | £120,000 | £5,000 |
Environmental Impact and Sustainability
Solar panels significantly reduce a manufacturing facility’s carbon footprint. A typical 500 kW system can offset about 500 tonnes of CO2 annually, equivalent to planting 25,000 trees.
- Renewable energy targets: Solar helps meet corporate sustainability goals and regulatory requirements.
- Reduced air pollution: By decreasing reliance on fossil fuels, solar improves local air quality.
- Water conservation: Unlike traditional power plants, solar panels require minimal water for operation.
Solar adoption also enhances a company’s reputation, appealing to environmentally conscious consumers and partners. This can lead to increased sales and improved stakeholder relations.
Energy Independence and Grid Reliability
Solar panels provide manufacturing facilities with a degree of energy autonomy. This independence from the grid offers several benefits:
- Consistent power supply: Solar reduces vulnerability to grid outages, ensuring continuous operations.
- Price stability: Protection against future electricity price hikes.
- Load management: Solar can be combined with energy storage for optimal load balancing.
During peak sunlight hours, excess energy can be fed back into the grid, potentially generating additional revenue. Some facilities achieve near self-sufficiency, using the grid only as a backup.
By reducing strain on the local power infrastructure, solar-equipped factories contribute to overall grid stability, benefiting the entire community.
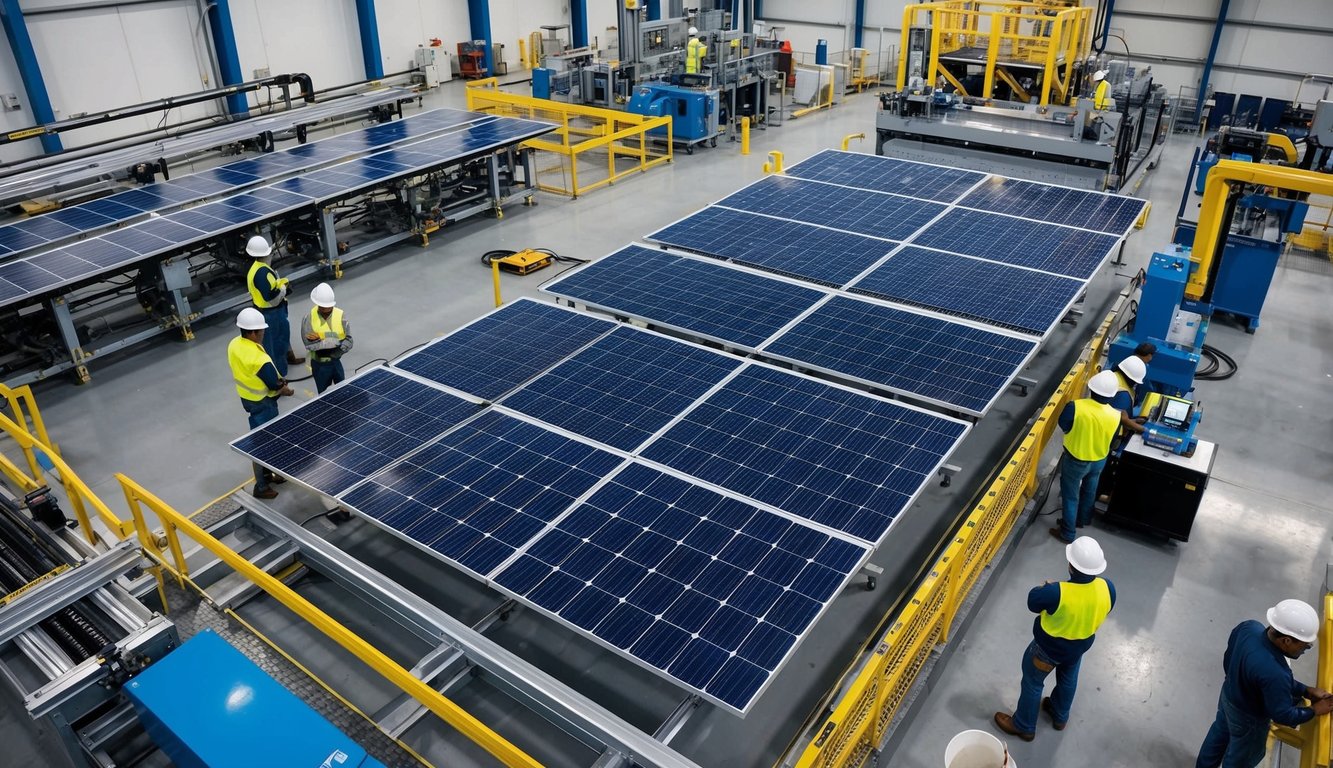
Engineering Considerations For Solar Implementation
Implementing solar panels in manufacturing facilities requires careful planning and technical expertise. Key factors include accurate load calculations, proper structural assessments, and seamless integration with existing power systems.
Load Calculations and System Design
Load calculations form the foundation of a successful solar installation. Engineers must analyse the facility’s energy consumption patterns to determine the optimal system size. This involves:
• Peak demand: Assessing maximum power requirements
• Daily usage: Calculating average energy consumption
• Seasonal variations: Accounting for fluctuations throughout the year
System design incorporates these calculations to specify the number and type of solar panels needed. Engineers must also consider:
• Panel efficiency: Selecting high-performance modules
• Inverter sizing: Matching inverter capacity to panel output
• Energy storage: Evaluating battery options for consistent power supply
Proper design ensures the solar system meets the facility’s energy needs whilst maximising return on investment.
Structural Requirements for Roof Mounting
Roof-mounted solar arrays require thorough structural analysis. Engineers must evaluate:
• Roof load capacity: Assessing if the existing structure can support additional weight
• Wind resistance: Designing mounting systems to withstand local wind conditions
• Waterproofing: Ensuring roof integrity is maintained after installation
Structural modifications may be necessary to accommodate solar panels. This could involve:
• Reinforcing roof trusses
• Installing additional support beams
• Upgrading roofing materials
Engineers must also consider panel orientation and tilt to optimise solar exposure. Proper mounting design prevents damage to both the roof and solar system, ensuring long-term reliability.
Integration With Existing Power Systems
Seamless integration of solar power with existing electrical infrastructure is crucial. Engineers must design:
• Interconnection points: Determining optimal locations to connect solar output
• Switchgear modifications: Updating electrical panels to accommodate new power sources
• Metering systems: Installing equipment to monitor solar production and usage
Power quality is a key consideration. Engineers implement:
• Voltage regulation: Ensuring stable power supply despite solar fluctuations
• Harmonics mitigation: Reducing distortions caused by inverters
• Fault protection: Updating safety systems to handle bidirectional power flow
Proper integration maximises the benefits of solar power whilst maintaining reliable operation of manufacturing equipment.
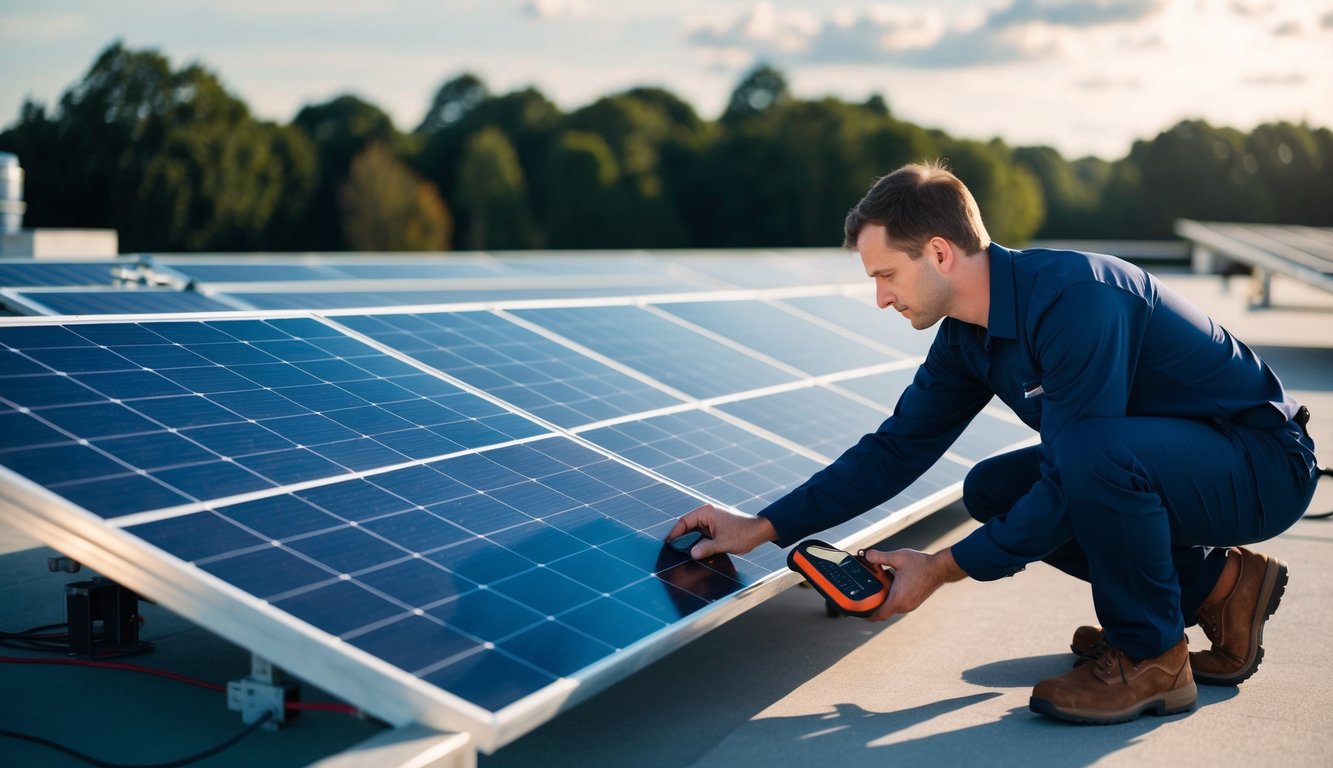
Maintenance And Performance Optimisation
Proper upkeep and efficiency enhancement are crucial for maximising solar panel output. Regular inspections, cleaning, and monitoring help ensure optimal performance and longevity of photovoltaic systems.
Regular Maintenance Schedules
Solar panel maintenance requires a structured approach. Cleaning is essential, with frequency depending on local conditions. In dusty areas, panels may need cleaning every 2-3 months, while in cleaner environments, annual cleaning might suffice.
Visual inspections should occur quarterly. Check for:
• Physical damage: Cracks or chips in panels
• Wiring issues: Loose connections or exposed cables
• Mounting stability: Secure fasteners and brackets
Trim nearby vegetation to prevent shading. Annually, have a professional inspect inverters, electrical systems, and overall panel performance. Keep detailed records of all maintenance activities for warranty purposes and to track system health over time.
Performance Monitoring Systems
Implement robust monitoring to track solar panel efficiency. Modern systems use sensors and software to provide real-time data on:
• Energy production: Daily, monthly, and annual output
• Panel efficiency: Individual and overall system performance
• Environmental factors: Temperature, irradiance, and weather impacts
Metric | Purpose | Frequency |
---|---|---|
Power output | Track energy generation | Continuous |
Voltage/current | Identify underperforming panels | Hourly |
Inverter efficiency | Ensure optimal conversion | Daily |
Automated alerts can notify you of sudden drops in performance, allowing for swift troubleshooting. Regular analysis of this data helps identify trends and optimise system output.
Troubleshooting Common Issues
Quick identification and resolution of problems maintain solar panel efficiency. Common issues include:
Reduced output: Often caused by dirt accumulation or shading. Clean panels and trim obstructing foliage.
Inverter faults: Check error codes and restart. If persistent, consult a technician.
Hot spots: Use thermal imaging to detect. May require panel replacement if severe.
Loose connections: Tighten all wiring connections annually to prevent power loss and potential fire hazards.
Degradation: Natural efficiency loss over time. Compare current output to initial specifications to gauge panel health.
For complex issues, engage certified solar technicians. Keep spare parts on hand for quick repairs, minimising downtime and maintaining consistent energy production.
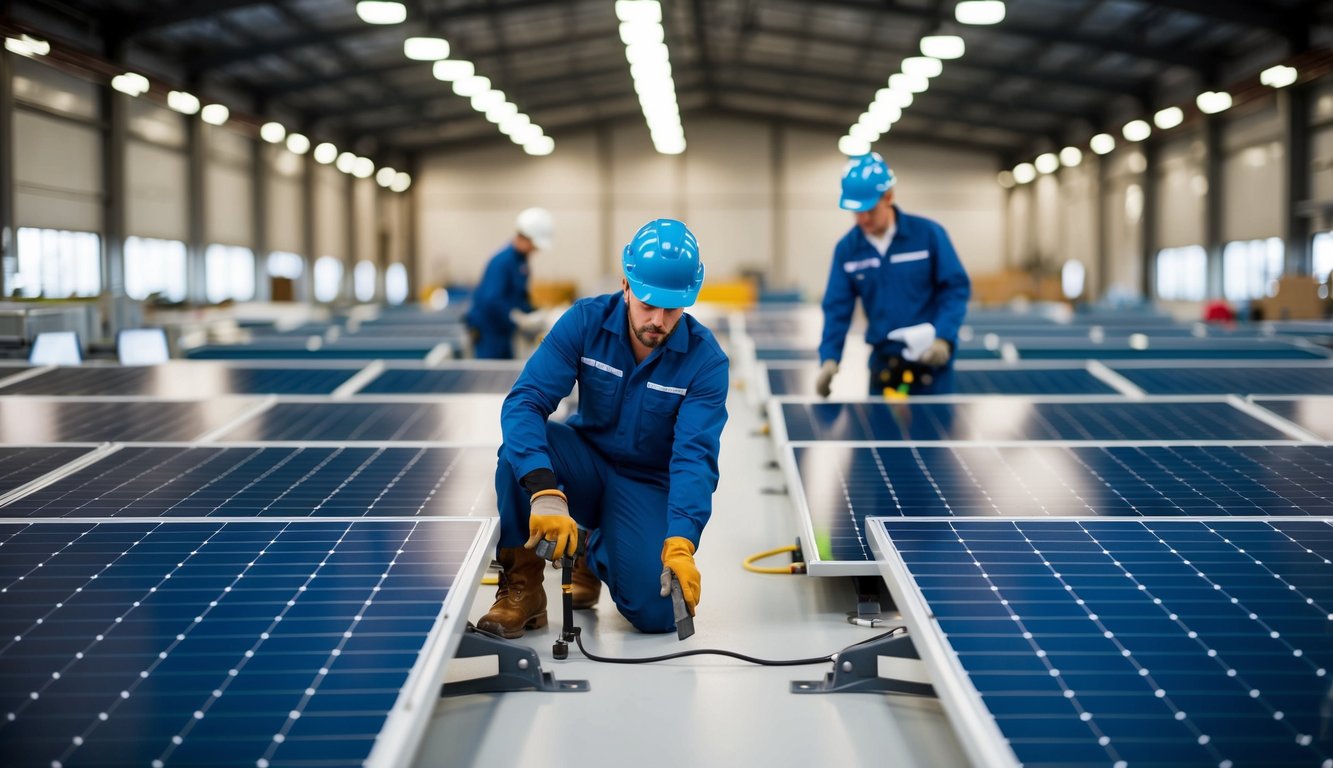
Regulatory Compliance and Standards
Solar panel installations for manufacturing and engineering facilities must adhere to strict regulations and standards. These ensure safety, efficiency, and proper integration with existing infrastructure.
Industrial Safety Requirements
Industrial solar panel installations require rigorous safety measures. Electrical safety is paramount, with proper grounding and insulation essential. Panels must withstand environmental stresses like wind loads and temperature fluctuations.
Fire safety protocols are crucial. Panels and mounting systems should be fire-resistant and not impede emergency access routes. Regular inspections and maintenance schedules are mandatory to maintain safety standards.
Worker safety during installation and maintenance is also critical. Proper personal protective equipment (PPE) and fall protection systems are required for rooftop installations.
Building Codes and Permits
Local building codes govern solar panel installations. These often include:
- Structural assessments to ensure roofs can support panel weight
- Setback requirements from roof edges and fire zones
- Height restrictions and visual impact considerations
Planning permission may be required, especially for ground-mounted systems or in conservation areas. Electrical work typically needs approval from certified inspectors.
The Microgeneration Certification Scheme (MCS) is vital for grid-connected systems in the UK. It ensures installations meet quality standards and are eligible for government incentives.
Energy Efficiency Certifications
Solar panels contribute to a facility’s overall energy efficiency. Several certifications reflect this:
- BREEAM (Building Research Establishment Environmental Assessment Method) assesses sustainability, including renewable energy use.
- Energy Performance Certificates (EPCs) rate building energy efficiency, with solar installations potentially improving scores.
- ISO 50001 certification for energy management systems can incorporate solar energy strategies.
These certifications can enhance a company’s green credentials and may be required for certain government contracts or planning approvals.
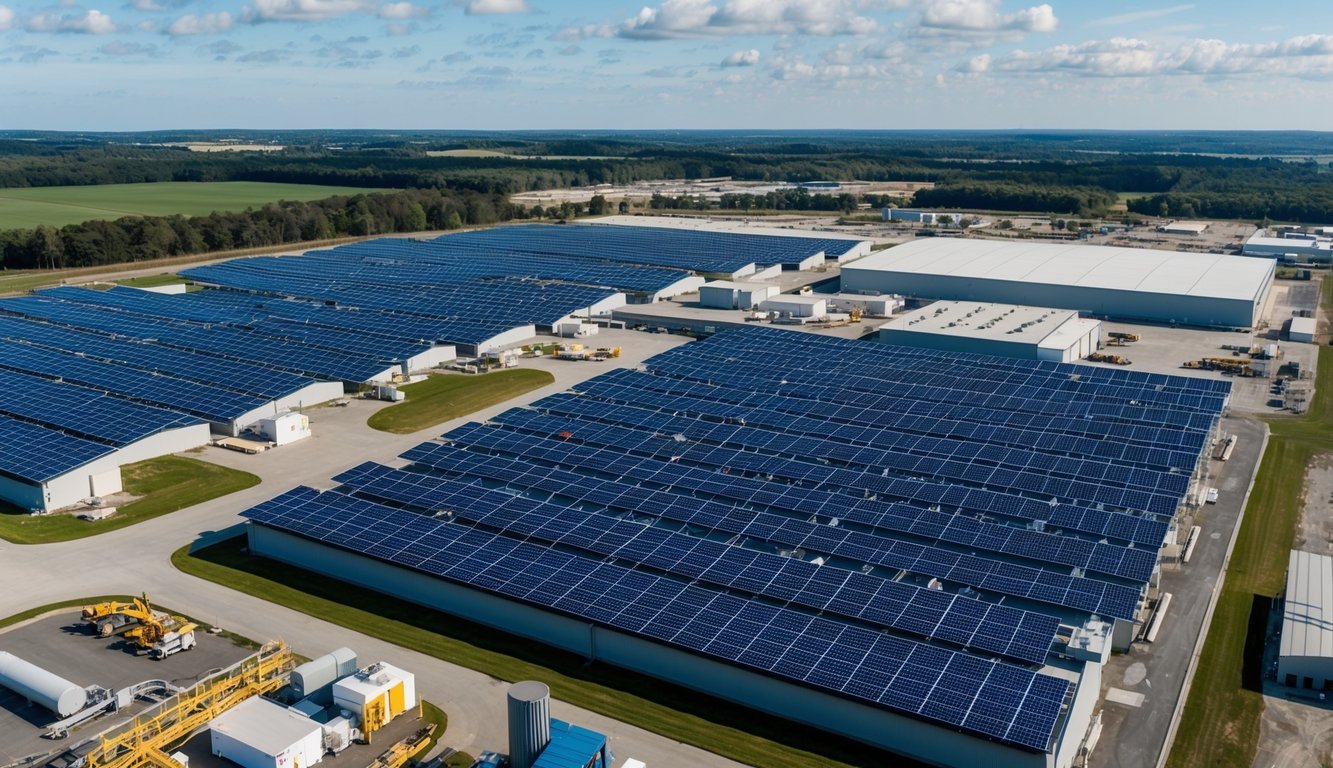
Future Trends In Industrial Solar Applications
Solar technology for manufacturing and engineering continues to advance rapidly. New innovations promise to revolutionise how factories and industrial facilities harness the sun’s energy.
Emerging Technologies
Perovskite solar cells represent a promising development. These cells offer potential for higher efficiencies and lower production costs compared to traditional silicon panels. Researchers are working to improve their stability and lifespan for commercial use.
Bifacial modules capture sunlight from both sides, increasing energy yield. As prices fall, more factories may adopt these to maximise roof and ground space.
Transparent photovoltaics could transform factory windows into power generators. This technology allows visible light through whilst converting ultraviolet and infrared rays into electricity.
Floating solar farms on reservoirs or treatment ponds provide an innovative solution for space-constrained facilities. These systems reduce water evaporation whilst generating clean energy.
Smart Manufacturing Integration
Solar power increasingly integrates with smart factory systems. Artificial intelligence optimises energy consumption by predicting demand and adjusting production schedules.
Internet of Things (IoT) sensors monitor solar panel performance in real-time. This data allows for predictive maintenance, reducing downtime and maximising efficiency.
Digital twins create virtual models of solar installations. Engineers use these to simulate different scenarios and optimise system design before physical implementation.
Microgrids combining solar, storage, and intelligent controls enhance energy resilience. Factories can operate independently during grid outages, ensuring uninterrupted production.
Energy Storage Solutions
Advanced battery technologies complement solar installations. Flow batteries offer long-duration storage ideal for overnight operations or cloudy days.
Thermal energy storage systems capture excess heat from industrial processes. This heat can be used later for manufacturing or converted back to electricity.
Hydrogen production via solar-powered electrolysis is gaining traction. Excess solar energy splits water into hydrogen and oxygen, providing a clean fuel for industrial processes or transport.
Pumped hydro storage presents an option for large-scale energy storage. Surplus solar power pumps water uphill, which is released through turbines when needed.
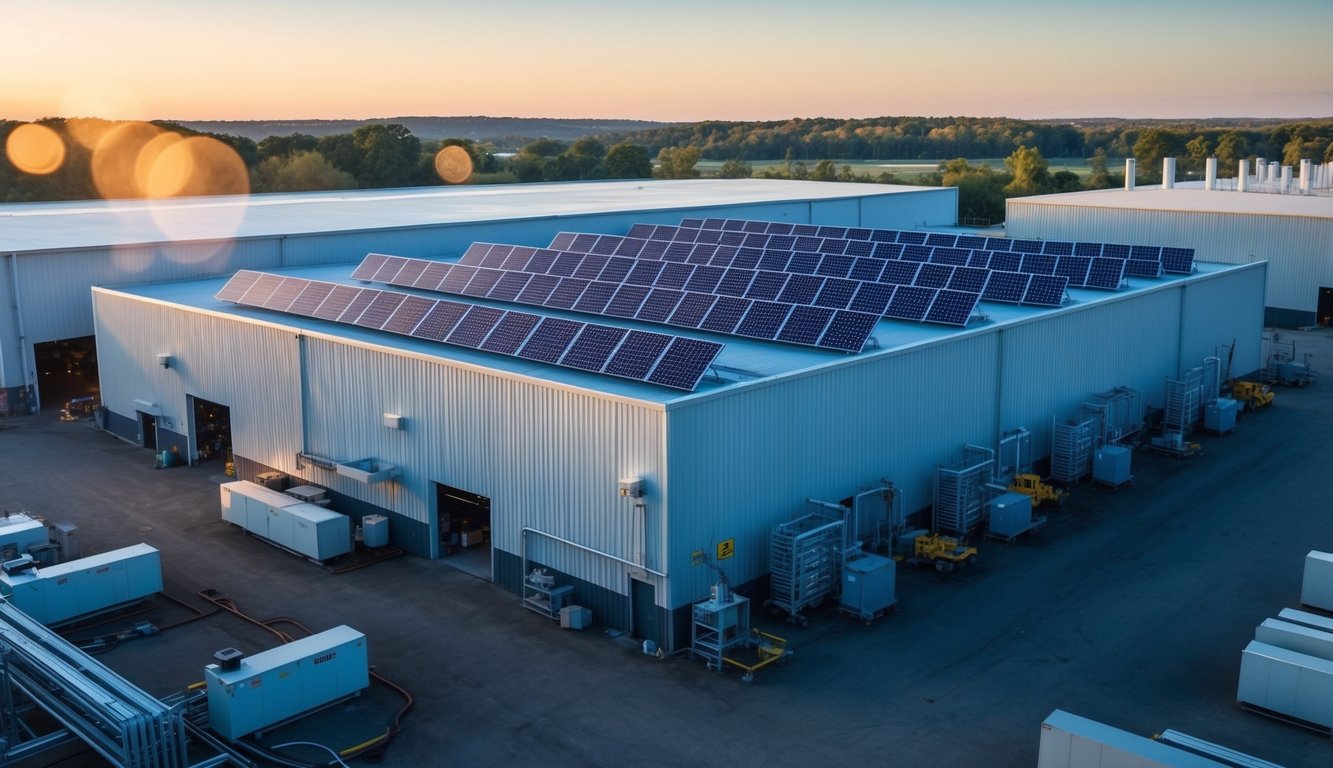
Cost Analysis And Financial Planning
Solar panel manufacturing involves significant financial considerations. Careful planning and analysis are essential for success in this sector.
Initial Investment Considerations
Setting up a solar panel manufacturing plant requires substantial upfront capital. The primary costs include purchasing machinery, securing facilities, and obtaining raw materials. Equipment expenses typically constitute the largest portion of the initial outlay.
Key equipment needed:
- Ingot growers
- Wafer slicers
- Cell production lines
- Module assembly systems
Facility costs vary based on location and size. A medium-sized plant may require 5,000-10,000 square metres. Raw material procurement, including silicon, glass, and metals, represents another major expense.
Labour costs for skilled technicians and engineers must also be factored in. Hiring and training staff is crucial for quality production.
Available Tax Incentives and Grants
Governments often offer financial incentives to promote solar manufacturing. These can significantly reduce overall costs and improve profitability.
Common incentives include:
- Tax credits: Reduce tax liability based on investment amount
- Grants: Direct financial support for research or expansion
- Subsidised loans: Low-interest financing for capital expenses
- Import duty exemptions: Reduced costs for imported equipment
Research local and national programmes to maximise benefits. Eligibility criteria and application processes vary, so thorough investigation is vital.
Some regions offer additional perks like discounted land or utility rates for solar manufacturers. These can provide substantial long-term savings.
Long-term Financial Benefits
While initial costs are high, solar panel manufacturing can offer strong returns over time. The growing demand for renewable energy drives consistent sales opportunities.
Economies of scale play a crucial role. As production volume increases, per-unit costs typically decrease. This improves profit margins and competitiveness.
Technological advancements can boost efficiency and reduce material costs. Investing in research and development often pays off through improved products and processes.
Diversification into related products, such as inverters or mounting systems, can create additional revenue streams. This helps mitigate market fluctuations in panel prices.
Conclusion
Solar panels play a crucial role in transforming manufacturing and engineering sectors. You can harness renewable energy to power your facilities, reducing operational costs and environmental impact. The integration of solar technology requires careful planning and expertise.
Implementing solar solutions offers numerous benefits:
• Cost savings: Lower electricity bills
• Sustainability: Reduced carbon footprint
• Energy independence: Less reliance on the grid
• Innovation: Adoption of cutting-edge technology
Quality control is paramount in solar panel production. Rigorous testing ensures optimal performance and longevity. As you consider solar adoption, consult with experts to tailor solutions to your specific needs.
The future of manufacturing lies in sustainable practices. Solar energy represents a significant step towards greener operations. By embracing this technology, you position your business at the forefront of industry innovation.
Remember, solar panel integration is an ongoing process. Regular maintenance and updates will maximise efficiency and return on investment. Stay informed about advancements in solar technology to continually improve your energy systems.
Frequently Asked Questions
Solar panels for industrial applications raise numerous queries about costs, production processes, and practical implementation. Let’s address some common questions to provide clarity on this technology’s role in manufacturing and engineering.
What are the initial and ongoing costs associated with installing solar panels for industrial purposes?
Initial costs for industrial solar panel installation typically range from £50,000 to £500,000, depending on system size and complexity. Ongoing expenses include periodic maintenance, which averages £500-£1,000 annually. Energy savings often offset these costs within 5-10 years.
In what ways is solar energy deployed within the transportation sector?
Solar energy powers electric vehicle charging stations and railway signals. Some trains use roof-mounted panels to supplement onboard power. Solar-powered boats and experimental aircraft demonstrate the technology’s potential in various transport modes.
Could you explain the process of solar panel production?
Solar panel production involves several steps. It begins with purifying silicon, which is then formed into wafers. These wafers are treated to create photovoltaic cells, which are assembled into modules. Finally, the modules are sealed and framed to create finished solar panels.
Which companies currently lead the market in solar panel manufacturing?
As of 2025, leading solar panel manufacturers include JinkoSolar, LONGi Solar, and Trina Solar. These firms dominate global production, with significant market shares in Europe and Asia. British companies like Oxford PV are making strides in next-generation solar technology.
How does engineering play a role in the development and optimisation of solar panel technology?
Engineering is crucial in improving solar panel efficiency and durability. Materials scientists develop new photovoltaic materials, while electrical engineers optimise power conversion. Mechanical engineers design robust panel structures to withstand environmental stresses.
Is it feasible for solar panels to power an entire manufacturing plant?
Powering an entire manufacturing plant with solar panels is challenging but increasingly feasible. Large-scale installations, combined with energy storage systems, can meet significant portions of a factory’s energy needs. However, most facilities still rely on grid power for consistent operation.